Profile Of Indian Foundry Industry
The Indian Metal casting( Foundry Industry ) is well established. According to the recent World Census of Castings by Modern Castings, USA India Ranks as 2nd largest casting producer producing estimated 7.44 Million MT of various grades of Castings as per International standards .
The various types of castings which are produced are ferrous,non ferrous,Aluminium Alloy, graded cast iron,ductile iron,Steel etc for application in Automobiles,Railways, Pumps Compressors & Valves, Diesel Engines,Cement/Electrical/Textile Machinery,Aero & Sanitary pipes & Fittings etc & Castings for special applications.However,Grey iron castings is the major share approx 70 % of total castings produced.
There are approx 4500 units out of which 80% can be classified as Small Scale units & 10% each as Medium & Large Scale units.Approx 500 units are having International Quality Accreditation.The large foundries are modern & globally competitive & are working at nearly full capacity. Most foundries use cupolas using LAM Coke.There is growing awareness about environment & many foundries are switching over to induction furnaces & some units in Agra are changing over to cokeless cupolas.
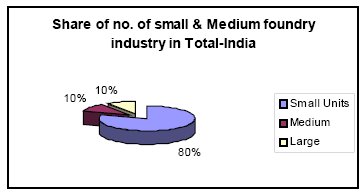
Exports
The Exports are showing Healthy trends approx 25-30% YOY as can be seen from the charts below.The current exports for FY 2005-06 are approx USD 800 Million.
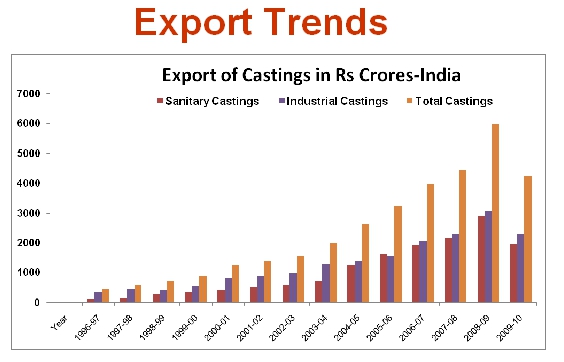
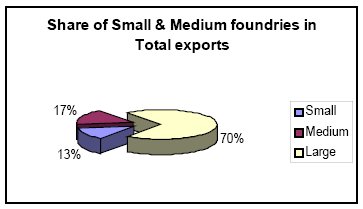
Employment
The industry directly employs about 5,00,000 people & indirectly about 1,50,000 people & is labour intensive.The small units are mainly dependant on manual labour However,the medium & Large units are semi/ largly mechanized & some of the large units are world class
Most foundries use cupolas using LAM Coke.There is growing awareness about environment & many foundries are switching over to induction furnaces & some units in Agra are changing over to cokeless cupolas.
Important Clusters
There are several foundry clusters .Some of the major clusters are as below.Each cluster is known for its type of products
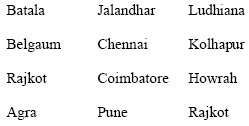
Product Mix
Grey iron is the major component of production followed by steel,ductile iron & non ferrous as Shown below
The Indian Foundry Industry is trying to focus on higher value added castings to beat the competition
Investments
India would need approx. $ 3 Billion in investment to meet the demand of growing domestic industry and strong export drive.
Following the economic reforms the Govt. of India has reduced tariffs on imported capital goods as a result the annual average amount of FDI is reported to have increased but is still one tenth of the annual FDI in China. The reforms also encourage the privatization of industry enabling foreign companies to invest or enter into joint ventures with Indian Foundries. FDI projects are permitted an automatic approval process. Several International corporate from USA, EU and East Asian Countries have increased overseas foundry operations in India. i.e. VOLVO foundries in Chennai and Suzuki in Haryana. Sundaram Clayton has joined hands with Cummins. Hundai Motors,
Delphi. Ford India, Tata-Cummins, GM and Ford have contracts of foundry products for export with a value of $ 40 Million.
Raw material & Energy
Since 2003 the steep increase in cost of raw materials and energy have resulted in the closure of approx. 500 units, Overall India is exporter of Pig Iron but must import Scrap metals and Coke etc. Cost recovery for material and energy is very difficult as most contracts are long term contracts with out any clause for price adjustment. India has to import coke & scrap.Moulding sand is locally available & India has an advantage on this account .
Energy cost typically vary between 12-15%
Labour
India has major competitive advantage over the foundry industries in the developed countries. The total labour cost account for 12-15%
Technology
Govt. of India ( GOI ) has encouraged technology transfer through JV with foreign Companies and GOI has cooperated with UNIDO with many foundry clusters. Indian foundry industry has an edge over China for producing complex machined and precision castings as per international quality standards. The GOI also helps upgrade foundry clusters. The clusters in Belgaum, Coimbatore and Howrah are undergoing modernization under the industrial infrastructure upgradation scheme.More of such clusters are likely to follow
The Institute of Indian Foundrymen has plans to strengthen and develop various foundry clusters.