ECOMELT GAS-FIRED COKELESS
FURNACE FOR CAST IRON MELTING:
COST-EFFECTIVE AND ECO-FRIENDLY OPERATION
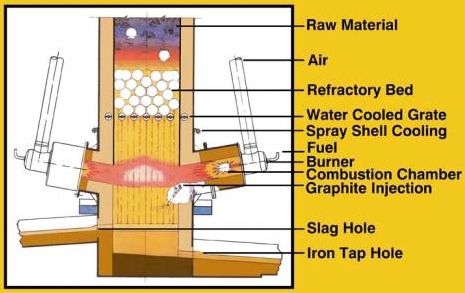
Development of the Cokeless Melting Furnace began in the UK at the foundry of Hayes Shell Cast Limited in the mid-1960s. A pilot furnace was built during 1967 to prove the ideas of melting cast iron with gas at a relatively low temperature and then superheating by some other means. Trials established that iron of suitable temperature and composition could be tapped directly from the furnace without any superheating. As a result one of the existing 5 tonnes per hour cupolas was converted to a gas-fired cokeless system in November 1970.
Features
In a conventional coke fired cupola the coke has three functions.
- It acts as a source of heat
- In the bed it superheats the iron as it trickles over the coke
- It acts as a source of carbon
In the Cokeless Melting Furnace these functions are provided by three different means:
- Heat is provided by the burners, which can be fired with a variety of fuels such as natural gas, diesel oil, propane or other suitable fuels.
- Superheating is done by the specially developed spheres that form the refractory bed. The Spheres are supported by a water-cooled grate consisting of specially designed mild steel tubes, which may be coated with refractory. The metal is superheated as it trickles over the spheres.
- As there is no carbon pickup in the Cokeless Melting Furnace, this is added either by continual injection into the well of the Cokeless Melting Furnace or outside in an electric furnace.
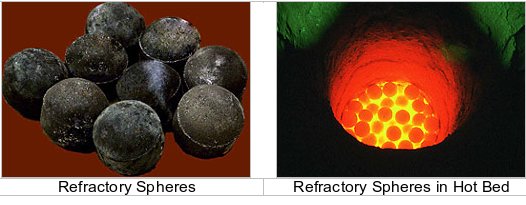
The Cokeless Melting Furnace is operated with partially reducing conditions. It is very important that the correct air/fuel ratio is maintained at all times otherwise the required temperature will not be achieved as the furnace temperature reduces steeply with both excess fuel and excess air condition. An automatic control system forms part of the main control panel and the air and fuel flows to each burner are also monitored.
Unit Melting
The Cokeless Melting Furnace technology can be applied in the traditional manner as a unit melter when high temperature metal of the right composition is available directly from the cupola into ladles for pouring into moulds.
This type of operation has been applied in many foundries in different countries but it is generally limited to smaller and medium size foundries operating up to 4/ 5 tonnes per hour and melting for up to 8 hours per day. In a unit melter fairly high tapping temperatures will be required. To achieve tapping temperatures of around 1450 to 1460 deg C a bed height of around 650 mm would be required. This means higher rate of consumption of spheres. However if lower temperatures are sufficient then the bed height can be reduced which will reduce the sphere consumption.
Since the spheres will not provide the necessary carbon, and since in Cokeless Melting Furnace there is approximately a 10% carbon loss during melting, with the usual charge make up, it will be necessary to add some carbon to the iron. A carbon injection unit, therefore, will be required which continually blows carbon into the cupola during melting. The rate of injection can be controlled.
Duplexing
A Cokeless Melting Furnace is a very efficient melting unit as cold material is added to the top; the metal is preheated as it moves down the shaft and after melting is superheated as it passes through the bed. If high temperature metal is required from a coke cupola the coke consumption is increased considerably. In the case of the Gas / Oil fired Cokeless Melting Furnace this also increases the consumption of the bed material, hence super heating is less economical in both cases.
An electric furnace is not a very efficient melting unit but once the metal is liquid the superheating of the iron is very efficient. Therefore melting iron in cupola at low temperature and superheating in an electric furnace is a very cost effective combination. This is called duplexing.
In case of duplexing a low bed of around 250 mm is used corresponding to only two rows of spheres which when new are approximately 150 mm in diameter. This drastically reduces the consumption of bed material – spheres. Reduced bed height reduces the tapping temperature but increases the melting rate. Therefore, compared with a unit melter, the overall gas consumption also reduces.
Advantages of Ecomelt Cokeless Melting Furnace
a) Coke not required:
India does not have reserve of good quality coking coal. We have to import coke from other countries. Use of Gas / Oil fired Cokeless Melting Furnace will eliminate the use of coke.
Gas is becoming available at various locations through out the country. To take advantage of the availability of natural gas in many parts of the country, Cokeless Melting Furnace should be used extensively. The Cokeless Melting Furnace can also be fired with LPG, or Light Diesel Oil.
b) Significantly Reduced or Zero Pollution:
The Gas fired Cokeless Melting Furnace for Iron melting was developed over 30 years ago and a comment passed about its performance in the early days is still very appropriate and probably more relevant, particularly in view of today's stringent pollution norms. The comment was "What does not come out the top is more important than the metal from the bottom".
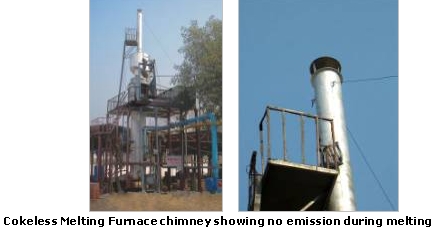
There is an increasing worldwide awareness of the impact that many processes can have on the environment. This is certainly true for foundries in India where the cost of meeting new regulations is significant.
A conventional coke cupola causes significant pollution. Besides suspended particulate matter, there are also carbon monoxide, carbon dioxide and sulphur emissions, none of which are good for the environment. If the cupola was converted to a gas fired Cokeless Melting Furnace there would be no visible emission, no sulphur emissions, carbon emissions approximately 1/6 that of coke operation, and less than 2% carbon monoxide in the waste gas. There will still be some dust emissions from the charge but these can be readily removed if required. Depending on regulations, there can be a considerable saving in capital cost as well as savings in running cost. In short there is a dramatic reduction in pollution level with SPM level being well within the Indian regulatory limit of 150mg/CuM.
c) Saving in Raw material:
Pig iron is the most expensive raw material in a cupola charge whereas steel scrap is cheaper. Foundries with coke cupola may be limited as to the amount of steel scrap they can use particularly if they are trying to obtain relatively high carbons. However, with the injection process used in the Cokeless Melting Furnace, this does not present a problem. Up to 30% steel scrap can be used in the charge. Similar percentage of sponge iron may also be used in Cokeless Melting Furnace, provided suitable arrangements to charge the same are made.
d) Other Advantages:
Once a cupola has been converted to Cokeless Melting Furnace, the foundry would be in a position to produce ductile iron and some graded iron without the need for an electric furnace. As this is a considerable growth area in India, it offers foundries an additional advantage over competitors who are still using a conventional coke cupola.
In case of gas fired Cokeless Melting Furnaces, the attack on lining is less and the life of lining is more. This makes maintenance easier and more economic. Longer melt campaigns of up to 48 hours are possible with minor modifications in refractory specification and water spray cooling of the shell near the burner area.
The foundry industry in India is rapidly expanding and many foundries have adopted electric melting, particularly for the production of ductile iron. For these foundries where expansion is being considered, the capital investment of installing a gas or oil fired Cokeless Melting Furnace could well be considerably less than adding additional electric furnaces. Liquid metal could be transferred from the Cokeless Melting Furnace to the existing electric furnaces where they would be used for superheating and recarburising the metal instead of purely melting. The existing electric capacity would be more than sufficient for any expansion as less than 100 kW hrs per tonne are required for superheating and recarburising whereas generally more than 600 kW hrs per tonne are required for electric melting.
e) Reduction In Melting Cost:
Tapping temperature has the main influence on economics, which as described above depends mainly on bed height. This influences the melting rate, which also effects the gas consumption.
With the unit melter operating at 1450 deg C, natural gas would be consumed at around 85 cu m per tonne with a typical sphere consumption of around 2.5%. In the duplex operation gas consumption comes down to 55 cu m per tonne with sphere consumption as low as 1%.
In both cases the amount of recarburiser depends on charge makeup and final analysis required. In duplex operation the recarburiser is added in the electric furnace with a recovery approaching 100%, whereas with a unit melter recovery is only around 50%. The cost will vary depending on type of metal being produced and whether graphite or a cheaper recarburiser is used in the process.
Although the price of coke, fuel and electric rates may vary from location to location, it is clear that the cokeless system can offer considerable economic benefits, with duplexing operation offering the highest saving.
Cokeless furnaces now in India
Since the invention of Gas Fired Cokeless Melting Furnace, many have been installed in various countries all over the world including UK, Germany, Japan, Korea, UAE, Iran, and Chile....
OPERATING ECONOMICS:
Ecomelt Gas-fired Cokeless Furnace for Cast Iron Melting
Indicative cost comparisons are provided for melting iron in a conventional furnace and in a Wesman-Taft gas or oil fired EcoMelt Cokeless Melting Furnace. Cost and consumption of fuel are taken from different sources and are average values. Fuel cost may vary from region to region, and also due to variation in design, furnace capacity and duration of melt campaign. For coke cupola, both price and consumption rate of coke will vary significantly depending on ash content. To arrive at your savings figure, please substitute your actual cost figures.
In addition to the savings below, there are substantial savings for an EcoMelt Cokeless Melting Furnace compared to a coke cupola as there is almost no need for pollution control equipment.
Melting Cost Per Tonne In Indian Rupees
Commercial Grade CI, 1350°C
Fuel: Natural Gas *Calorific value 9000 KCal/m3
COKE CUPOLA:
Coke 12% @ Rs. 13000 per MT: Rs. 1560
ECOMELT COKELESS MELTING FURNACE:
Natural Gas 60 CuM* @ Rs 12 per CuM Rs. 720
Sphere 1.5% @ Rs. 25000 per MT Rs. 375
Recarburiser 1% Rs. 14000 per MT Rs. 140 (petro carbon added)
TOTAL COST OF ECOMELT Rs. 1235
SAVINGS WITH ECOMELT Rs. 325 per MT
Graded CI, 1400°C
Fuel: Natural Gas *Calorific value 9000 KCal/m3
COKE CUPOLA:
Coke 17% @ Rs. 13000 per MT: Rs. 2210
ECOMELT COKELESS MELTING FURNACE:
Natural Gas 75 CuM* @ Rs 12 per CuM Rs. 900
Sphere 2% @ Rs. 25000 per MT Rs. 500
Recarburiser 1% @ Rs. 32000 per MT Rs. 320 (graphite powder added)
TOTAL COST OF ECOMELT Rs. 1720
SAVINGS WITH ECOMELT Rs. 490 per MT
Induction Melting Of Ductile Iron
Versus Duplexing With EcoMelt
Fuel: Natural Gas
INDUCTION FURNACE:
Electricity 600 KWH @ Rs. 5 per KWH Rs. 3000
ECOMELT COKELESS MELTING FURNACE AT 1300°C:
Natural Gas 55 CuM * @ Rs 12 per CuM Rs. 660
Sphere 1.5% @ Rs. 25000 per MT Rs. 375
Electricity 80 KWH @ Rs. 5 per KWH Rs. 400
Recarburiser 0.5% @ Rs. 32000 per MT Rs. 160 (graphite added in induction fce)
TOTAL COST OF ECOMELT Rs. 1595
SAVINGS WITH ECOMELT Rs. 1405 per MT
Induction Melting Of Ductile Iron
Versus Duplexing With EcoMelt
Fuel: LPG
INDUCTION FURNACE:
Electricity 600 KWH @ Rs. 5 per KWH Rs. 3000
ECOMELT COKELESS MELTING FURNACE AT 1300°C:
LPG 40 KG @ Rs 35 per kg Rs. 1400
Sphere 1.5% @ Rs. 25000 per MT Rs. 375
Electricity 80 KWH @ Rs. 5 per KWH Rs. 400
Recarburiser 0.05% @ Rs. 32000 per MT Rs. 160 (graphite added in induction fce)
TOTAL COST OF ECOMELT Rs. 2335
SAVINGS WITH ECOMELT Rs. 665 per MT
Induction Melting Of Ductile Iron
Versus Duplexing With EcoMelt
Fuel: LDO
INDUCTION FURNACE:
Electricity 600 KWH @ Rs. 5 per KWH Rs. 3000
ECOMELT COKELESS MELTING FURNACE AT 1300°C:
LDO 46 Ltrs @ Rs 33 per Ltr. Rs.1518
Sphere 1.5% @ Rs. 25000 per MT Rs. 375
Electricity 80 KWH @ Rs. 5 per KWH Rs. 400
Recarburiser 0.05% @ Rs. 32000 per MT Rs. 160 (graphite added in induction fce)
TOTAL COST OF ECOMELT Rs. 2453
SAVING WITH ECOMELT Rs. 547 per MT
Source: Wesman Group of Companies, Kolkata